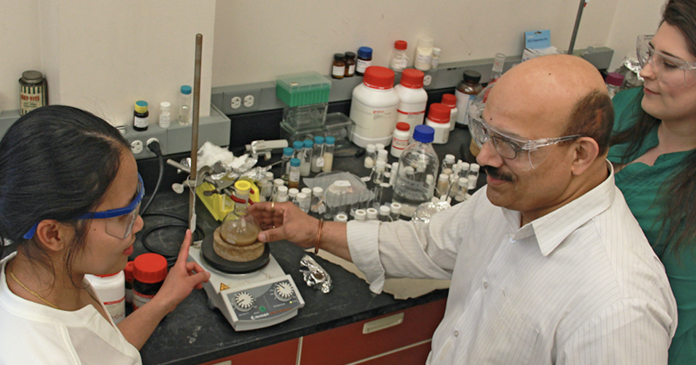
A technology born from University of Louisville research uses spent distillers’ grains, corn and waste wood to create a low-calorie sugar substitute.
And it gets sweeter: the process also results in a bio-mass “coal” alternative that burns up to 20 times cleaner than the regular stuff.
The technology was invented at the UofL Conn Center for Renewable Energy Research, biomass conversion and biofuels group in collaboration with Michael Nantz and his team in the UofL chemistry department. The newly-issued patent for the technology is now licensed to Louisville-based startup, BioProducts, which is working to get it to market.
Brian Walsh, the company’s CEO, said the potential environmental benefits of the technology are huge. According to the U.S. Energy Information Administration, burning traditional coal can cause emissions linked to smog, acid rain and other negative environmental and health side effects
“There’s a better way to do it,” he said. “We don’t have to harm the earth. We don’t have to pollute.”
The process isolates xylose – a low-calorie sugar from the biomass. Xylose sugar is widely used as a diabetic sweetener in food and beverage applications. It is also used as a diagnostic agent to observe malabsorption in the gastrointestinal tract.
Once the xylose is extracted, the team turns the remnant agriculture waste products into a cleaner “drop-in” replacement for coal – a “bio-coal” product.
BioProducts licensed the technology from UofL’s Commercialization EPI-Center, which handles intellectual property resulting from university research and forges partnerships with companies for commercialization.
“I’m blown away with how well UofL does integrating technology with business leaders,” Walsh said. “I’ve never seen anything like it. I don’t see other universities doing that better.”
Dr. Jagannadh Satyavolu, theme leader for biomass and biofuels research at the UofL Conn Center, led this research effort and is the founder of BioProducts. Energy and value creation from waste products are his specialty.
In the past, Satyavolu has partnered with industry to accelerate the commercialization of multiple bioproducts made from wood and agricultural biomass materials. His bio-coal work has been partly funded by U.S. Endowment for Forestry and Communities. Dr. Satyavolu is continuing his bio-coal research work with Oregon Torrefaction LLC, John Day, Oregon and other industry partners.
The process technology behind those products, as with the technology licensed by BioProducts, was torrefaction — essentially, “roasting” the biomass material to remove moisture and certain volatile compounds. A densification step needs to follow torrefaction to make the product denser, turning it into a coal replacement brick that’s easier to store and ship.
He said the xylose work started about seven years ago, after he took on a pilot project to find new uses for spent distiller’s grain — something Kentucky has in spades — and for corn. Walsh said the product could also create an additional revenue stream for farmers who might otherwise lose money on their agriculture waste.
“We’re always looking for new opportunities to add value and lower the cost of biofuels,” Satyavolu said.